SCDigest Editorial Staff
SCDigest Says: |
There are a series of factors contributing to the logistics problems for exporters. The drop in capacity, tours, and stops is the primary factor.
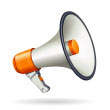
Click Here to See Reader Feedback
|
We’ve been here before, but this time it’s a little different.
In the first half of 2008, a still relatively strong global economy plus a falling US dollar led to a surge in US exports – often from middle America or other locations far from a major US port. The result – manufacturers often had trouble getting shipping containers to their factories to move the goods. (See For Want of a Box, the Export Order was Lost.)
The problem is now back, but in a somewhat different form. The tremendous collapse in ocean shipping volumes and rates have led major carriers to significantly cut back on capacity by mothballing or even scrapping vessels, dropping routes, and decreasing sailing speeds.
The unforeseen result: many of the same far from port shippers as well as other exporters are again having difficulty finding containers and timely shipment options, even as overall there is still much excess capacity in the market. This is happening as US exports are on the rise, and the Obama administration has pledged a major effort to increase US export levels.
“American producers of everything from hazelnuts to cardboard are complaining they can't get their goods shipped in timely fashion,” the Wall Street Journal wrote in a story about this last week. “Eighty rail cars filled with dried peas sat for weeks on train tracks outside Seattle, waiting for a ship to India. Wheat for Asia is stuck in a warehouse in North Dakota.” It found a soy bean famer in Minnesota is sometimes waiting 3-4 weeks longer than before to get his crop shipped to Asia.
There are a series of factors contributing to the logistics problems for exporters. The drop in capacity, tours, and stops is the primary factor; many carriers are simply sailing existing ships less often, and dropping port stops. French giant CMA-CGM, for example, decreased its total shipping capacity to East and West coast US ports by 22% last year and dropped Mobile, AL altogether from its ports of call.
Speed is another factor, as carriers have slowed speeds by 33% or more to reduce fuel costs amidst the brutal pricing and volume environment. That means each voyage takes longer to and from the US, adding days even when a shipper can secure a container and shipping date.
Finally, the ocean carrier schedules and port terminal operations have been built around the demand for US imports, not exports, leading to issues for shippers. For example, the Los Angeles Harbor Grain Terminal lacks enough space to handle the volume of exports now coming from farmers in the Midwest.
The WSJ cites the case of giant pork producer Smithfield Foods Inc., which used to ship to Asian customers from ports in the Northwest such as Seattle and Tacoma.
Now, however, ships and containers are in short supply there, so Smithfield is transporting pork raised in the Midwest to Houston and putting it on vessels that go through the Panama Canal to get to Asia. The result: higher costs and of 7-10 days longer to get to customers.
As the examples suggest, the problems are most acute in the agricultural sector.
"There are not enough ships or containers to handle the exports that the world wants to buy from us. This situation is becoming more dire by the day," says Peter Friedmann, executive director of the Agriculture Transportation Coalition, an industry group, noting that unlike branded products, buyers can easily go elsewhere if the US can’t deliver.
Story Continued Below
|