While putaway, picking, etc., are the most obvious and generally most critical tasks to consider, Kozenski says the maximum value will be achieved if the task engine is looking across all types of work in the DC in its pool of work to be assigned. This is especially true when the option of “task interleaving” is introduced. Task interleaving involves linking different types of tasks to a given operator, such as a full pallet putaway with a full pallet replenishment for a case picking area.
This is as opposed to workers focusing only on single tasks, such as putaway, which would mean driving back empty to receiving after each bit of work.
Using the task management engine, the system could instead identify that there is a storage location for the second task that is close to the putaway location from the first task, then assign that task to the putaway operator, reducing the amount of empty travel versus single threaded work assignment.
“With a broad list of possible tasks, the operation still has the option of which tasks to interleave and which to not,” Kozenski said. However, the more tasks that are included in the tasking pool, the greater the opportunities to efficiently combine tasks. (See graphic below.)
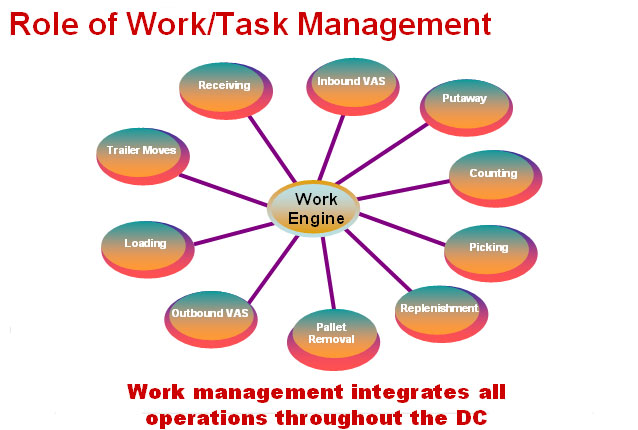
Kozenski also says that with more dynamic DC operations, including use of cross docking or flow through and lots of value-added services, the financial value of task interleaving is usually enhanced.
“The configurable workflows associated with inbound and outbound services in the DC have had a dramatic impact on the use of task interleaving,” Kozenski said. “For example, there might be a few more touches of things that have to occur between the unloading of a truck and putaway. Or, there might be things that have to happen between when an order is picked and when it is packed and loaded. Those will all create tasks that have to be embedded in the task interleaving strategies.”
Designing a DC for Task Interleaving
Most companies think about how to use tasking and task interleaving within the facility that they have. But, in many cases, it may be worth considering the potential to maximize use of interleaving when designing a new DC, or to evaluate layout or process changes in an existing DC to maximize productivity.
That’s what one large food company did when it implemented task interleaving, Kozenski said on the broadcast.
Like most companies, the DCs this company ran had all its receiving doors on one end of the building and its shipping doors on the other.
But the company wanted to link receipts from its factories with truck staging and loading. So, it reconfigured its doors into sets of five receiving and five loading docks each. By doing that, it was able to achieve double-digit productivity gains in these operations, Kozenski said, since the putaway task was so close to the drop off point for loading.
“You really need to look at your DC layout and flows to maximize task interleaving potential,” Kozenski said.
Should more companies look at DC flows and layouts to perhaps better utilize task interleaving potential? When does interleaving make sense and when does it not? Let us know your thoughts at the Feedback button below.
SCDigest is Twittering! Follow us now at https://twitter.com/scdigest |