Having flexibility, in theory, should provide a number of advantages. Transportation costs should be reduced by producing more products closer to customers. Variable demand can also be better managed as a result of more flexible production capacity and also shorter transportation lead times.
Using this framework and supply chain network modeling software, Simchi-Levi helped one food and beverage industry company determine its optimal supply chain flexibility strategy, which also demonstrates the core principles.
Starting with a baseline analysis of the company’s current “1X” capabilities, an analysis was performed to see the impact of adding various levels of flexibility into the manufacturing network.
The analysis was, of course, complex and sophisticated, but is nicely summarized on the chart below. The key point, as shown in the graphs on the left side of the illustration, is that total supply chain costs take a sharp drop when moving from 1X to 2X flexibility, but flatten out significantly after that. Since there is significant investment required to gain these additional levels of flexibility, the ROI from that investment is unattractive, making the simple 2X flexibility choice the optimal supply chain network strategy. The relatively modest investment to get 2X flexibility delivers about 80% of the total supply chain benefit of total flexibility, but at much lower upfront investment.
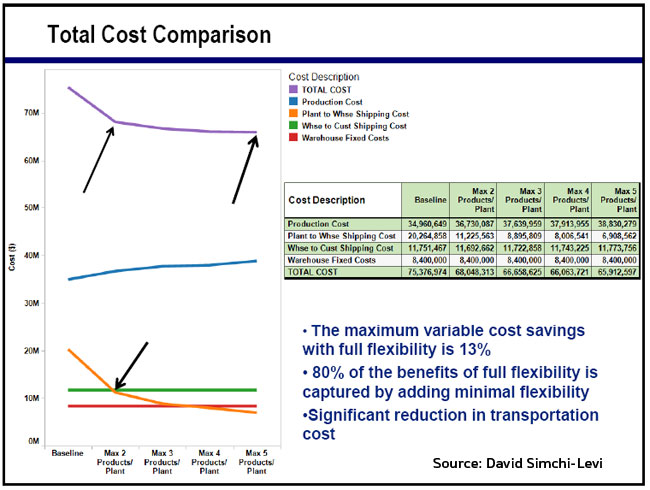
Simchi-Levi says that 2X flexibility remained the right choice for the company when looking at several different scenarios in terms of demand changes and volatility. He says that while sometimes somewhat higher levels of flexibility may be the best choice, “total flexibility” almost never is.
Does Simchi-Levi’s analysis surprise you? Is this a good way to look at supply chain network flexibility? Let us know your thoughts at the Feedback button below.
SCDigest is Twittering!
Follow us now at https://twitter.com/scdigest |