Is Lean a salvation for manufacturers, or a set of tools that can be useful but is often overhyped?
A little of both?
Lean manufacturing and Lean supply chain thinking have been incredibly powerful forces, and radically transformed hundreds of companies and the thinking of a broad swath of the manufacturing and supply chain industries.
Yet, at the same time, there has been some doubt and disappointment. Many have questioned whether Lean has been taken too far in many cases and left companies vulnerable to supply chain disruptions and customer service issues.
Gilmore Says: |
I think a few of the larger consultants have put a toe into the Lean practice water, but I don’t think most of them have gotten much more than their feet wet – not sure why that is.
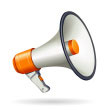
Click Here to See
Reader Feedback |
I bring this up, in part, as we usually do, to summarize what we’ve done in the latest Supply Chain Digest Letter on Lean Manufacturing. Many thousands of you should have received a copy in the mail, but if you didn’t and would like an electronic copy, or you would like to access a wealth of other resources, you can find them at our Lean Manufacturing Resources page.
Consider a company like Danaher, a growing industrial giant, which has made its custom version of Lean a science and an incredibly powerful driver of profits.
A couple of years ago, I happened to sit right next to a gentleman named Jim Britt, at the time a McKinsey Lean consultant who I believe has subsequently gone elsewhere. (Be forewarned, if you sit next to me on a plane, you are likely to receive a friendly interrogation.)
Britt (a very knowledgeable person) referenced to me the Lean story of Danaher, a company where he had once been a plant manager. At the time, I frankly had not heard of Dahaner, but it turns out the company has one of the most powerful Lean strategies on the planet. Business Week had this to say about Danaher and Lean in 2007:
“Danaher is a prolific acquirer, averaging about a deal per month. These “conglomerateurs” have built their portfolio not by buying undervalued companies and holding them but by imposing on them the "Danaher Business System." DBS, as it's called, is a set of management tools borrowed liberally from the famed Toyota Production System. Before a deal, Danaher executives tour plants and search for ways to improve performance. They estimate how wide an acquisition target's profit margins could get, given the Danaher treatment.”
Think about it – Danaher executives can tour a plant, and make a quick, but apparently very accurate, assumption about the improvements that could be achieved from going Lean. That smells like opportunity for most other companies right now, especially right now, trapped within their own factories and supply chains.
Britt, in fact, told me that he often did the same, walking around a factory and seeing dozens of things that could be quickly addressed with a little Lean treatment.
But Lean isn’t a panacea. Just the fact that we now have Lean Six Sigma, as companies such as 3M have vigorously pursued, says Lean alone may not be enough. Now it appears we even have something called “TLS,” which adds in Eli Goldratt’s Theory of Constraints (TOC) methodology as another tool, usually front-ending TOC before both Lean and Six Sigma (TOC, Lean, Six Sigma).
And the reality is that Lean programs often don’t deliver results, or get implemented a bit, but then not really carried forward. As a recent AMR Research report observed, “Most manufacturers we interviewed confine their Lean projects to a single plant, often right down to a production line or product area.”
Then there is the issue of technology and Lean. Clearly, some Lean consultants don’t want any part of it, but I think that is not right, or certainly not always right.
I don’t disagree with i2’s Aamer Rehman, who says that “manual Lean methods of the past have proven to be inconsistent and inadequate, and companies are looking for sophisticated, but not complex, solutions to support key operational aspects of Lean.”
This seems to me to be true for two reasons: First, the growing complexity of most factories in terms of product mix, routings, etc., that make it hard/impossible for the traditional tools of Lean to really well handle unaided.
Second, I don’t think (though some may dispute) that traditional Lean tools well handles the increasing outsourced/virtual world most manufacturers live in. A Kanban card is hard to see from across the street or across the ocean. Collaborative and visibility tools are essential to make a manufacturing operation dependent on partners run in a Lean-like fashion. In fact, the original source of Lean thinking itself, Toyota and its Toyota Production System, has recently announced several plans to improve partner connectivity and collaboration.
Certainly, I think you also need the foundation of a strong data collection capability to ensure accurate and timely information flow on the shop floor.
The Lean consulting environment is also interesting to me. It seems to me it is still almost totally dominated by boutique or smaller firms. I think a few of the larger consultants have put a toe into the Lean practice water, but I don’t think most of them have gotten much more than their feet wet – not sure why that is.
My personal belief is that Lean is a great thing, but that, for a variety of reasons (which we discuss in the Letter), it fails to reach its potential in far too many companies.
But the examples of Danaher, 3M and many others where Lean has provided outsized benefits can’t be ignored. We are entering into a “new world order,” and how companies themselves will shake out and how Western manufacturers will fare against those in China and other low-cost countries could go in several directions, I think.
To prosper, it will take something like Lean 2.0. Maybe we’re already on Lean 3.0 or something and I don’t know it. While the results aren’t always what’s expected and can often be taken too far (risk), if there has been a better time to get Lean right, I am not sure when that has been.
Think you will enjoy our excellent Lean Letter and other information. Find Resources page again here: Lean Manufacturing Resources. I’ll be honest that we are very proud of these SCDigest Letters and hope you will take a look.
What in your view has been the Lean track record in manufacturing? What are the key factors in success or mediocrity? Is it time for Lean 2.0? What about Lean and technology? Let us know your thoughts at the Feedback button below.
Let us know your thoughts at the Feedback button below.
|