|
|
|
|
 |
Supply
Chain by the Numbers |
|
|
|
- Oct. 18, 2013
|
|
|
|
|
|
|
|
US Bridges are Broken; Family Dollar Gets Aisle-Ready; Major US Aluminum Plant to Kick the Can; More Death in Bangladesh |
|
|
|
|
|
|
|
Number of workers killed in yet another apparel fire tragedy in Bangladesh two weeks ago, in a blaze that took the life of the general manager of the Aswad garment outside Dhaka. That after the enormous tragedy of the collapse of a building in Bangladesh earlier this year that was home to several apparel operations, and in which about 1100 people were killed in one of the greatest industrial disasters ever. There are rival plans by US and European retailers and brand companies to improve factory safety in Bangladesh, but the companies are mostly still working out the details.
|
|
|
|
|
|
|
$1800 |
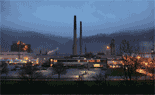 |
Approximate price per ton for aluminum right now, down from around $2600 two years ago, amidst a global glut of the metal. That low price has consequences, and this week Ormet, the US' fourth largest aluminum producer, announced it is closing its Hanibal, OH smelter and selling the operations to whomever it can. The key issue: electricity costs, which account for 25-33% of the smelter's operating budget. Ormet had been getting energy subsidies from the state to allow it to weather the aluminum price storm, and asked for more to enable it to switch over to cheaper natural gas power, but its request were denied. The plant employed some 1200.
|
|
|
|
|
|
|
|
 |
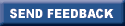 |
|
|
|