Stock and Mulki first identified five steps in the reverse logistics process:
(1) Pre-receipt: Providing authorization, labeling and other process elements to customers or consumers wanting to return product;
(2) Receiving: Unloading and distribution of product returns to processing centers;
(3) Processing: Activities such as data entry and issuing customer credits;
(4) Sortation: Inspection and routing of returns to disposition point; and
(5) Disposition: Putting the product back into inventory or temporary storage, repackaging, repair, refurbishing or remanufacturing.
The first step is generally handled by the company’s customer service group or through “self-service” by the customer or consumer. Some retailers simply send product back to manufacturers and take a credit against the manufacturer.
Of the next four steps that involve activity at the distribution center that will process the returns, the survey results found that of the total processing effort, on average, survey respondents spend about 31% of their total time on the “processing” step, followed by 26% each on sortation and disposition, and about 17% on receiving.
Perhaps surprisingly, and contrary to the researchers’ expectations, very few companies (at least in this survey group) used third party returns processing services. As can be seen in the chart below, the vast majority of manufacturers, retailers and wholesalers managed returns processing “in-house.”
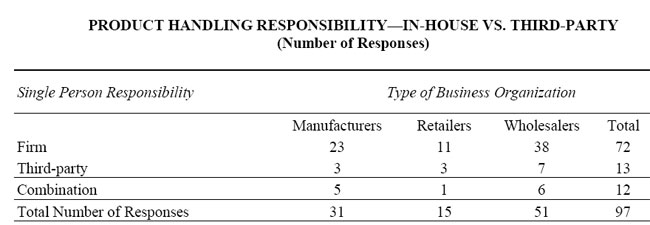
Source: Stock and Mulki, Journal of Business Logistics
Recovery Rates are High
In general, the research found that companies were generally able to recover a large percentage of the returned items’ value, whether through putting an item directly back into stock, or doing so after some modest amount of processing. Retailers and wholesalers, however, were able to, on average, recover much more of the total value than manufacturers.
As seen in the chart below, for example, 68.7% of retailers, on average, are able to recover at least 76% of the value of the returned goods, versus 61% for wholesalers and 38.3% for manufacturers (percentage added by SCDigest and represent percentages vertically, by sector). Conversely, about 37% of manufacturers recover less than 50% of the value.
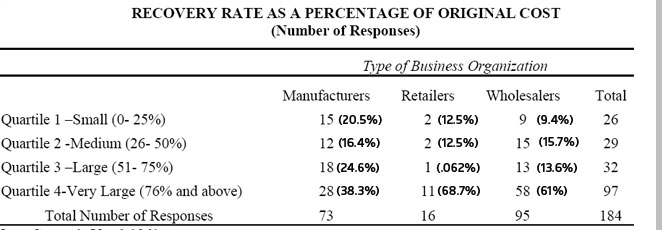
“In this study, product returns processing enabled many organizations to recover a high percent of the original cost of the products. In some instances, the recovery rates exceeded 80%,” Stock and Mulki note. “Such levels of recovery have not been widely reported previously. In fact, the typical level of 60-65% recovery rate is higher than expected given previously published data. This validates the importance of efficient and effective product returns processing for improving profitability within organizations.”
Source: Stock and Mulki, Journal of Business Logistics
The research also showed that a fairly high percentage of respondents in retail used metrics for tracking returns management efficiency and effectiveness. The paper used the term “standards,” though it appears that they really mean “performance metrics” as opposed to true “engineered” standards.
Regardless, as shown in the chart below, manufacturers are not yet active adopters, on average, of metrics for returns processing.
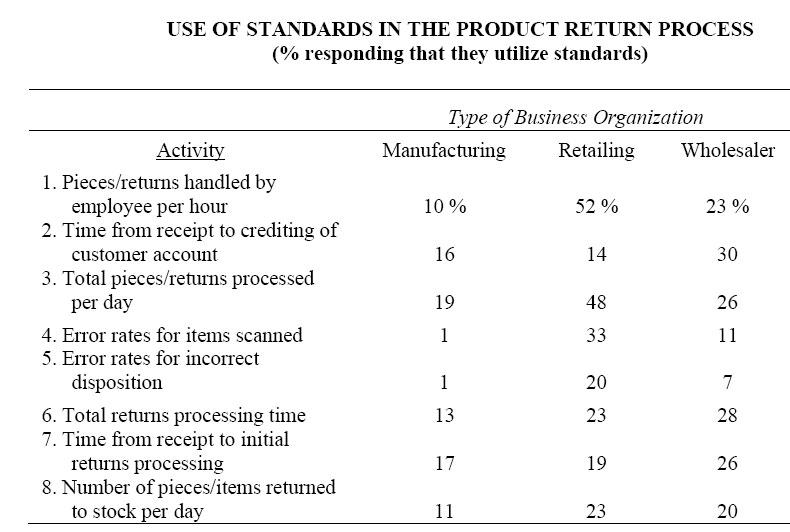
Source: Stock and Mulki, Journal of Business Logistics
The researchers conclude by noting “good product returns processing can result in improvements in profitability through cost reductions and higher product recovery rates.” They add that "Organizations with excellent product returns processing capabilities (defined as those having processes that are both efficient and effective) can have a potential competitive advantage, which gets larger as the magnitude of product returns increases.”
However, “The best way of optimizing the product returns process is to not have returns at all—referred to as returns avoidance. Return avoidance policies aimed at minimizing product returns are becoming popular. These strategies use customer education programs that focus on training the customer in the proper operation and use of the product.”
Any reaction to this data? Do you think reverse logistics really is an area of opportunity – or is it over rated? Do we have enough data to really understand the ROI for investment there? Let us know your thoughts at the Feedback button below.
SCDigest is Twittering!
Follow us now at https://twitter.com/scdigest |