(Manufacturing Article - Continued)
Employees at the larger companies averaged 98 cents (US dollars) per hour in total compensation in 2004. Those in established, but smaller, companies earned only half that much, at 49 cents US per hour.
Perhaps surprising to some, the level of benefit costs in China as a percent of hourly compensation is comparable to, or even greater than, those of Western countries. There are a variety of “funds” for health care, unemployment benefits, housing, pensions and other categories that both employees and employers must contribute. Different municipalities and provinces sometimes layer on their own individual required fund contributions, though the report notes that, in both cases, employers often evade their contributions. Nevertheless, the report says these benefits or additional contribution costs averaged nearly 30% of base wage compensation for Chinese employers in 2004.
The total hourly compensation varies significantly across different manufacturing sectors, according to the research. While the average across all sectors was 98 cents US per hour, as shown in the illustration below, these costs ranged from $4.37 per hour in the state-controlled tobacco production industry, to $1.35/hour for equipment manufacturing, to just 78 cents/hour in paper production.
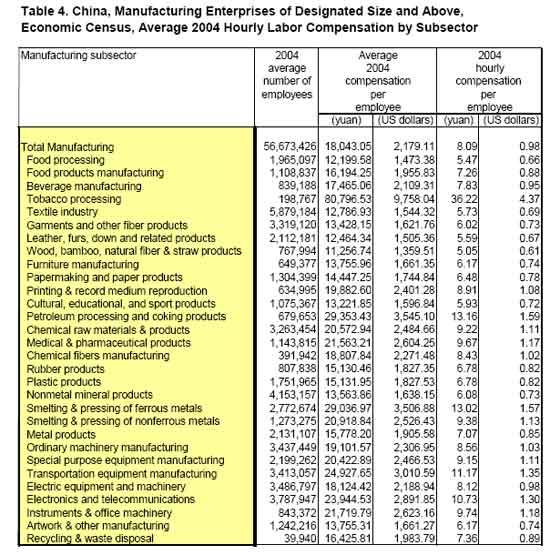
Source: Corporate Executive Board
Differences by Region
The largest concentrations of employees in state-owned and large-scale manufacturing enterprises are in Guangdong province (contiguous with Hong Kong and Macao in southern China), provinces at the mouth of the Yangtze River (Jiangsu, Zhejiang, and Shanghai), and the Shandong province, another large coastal province. In provinces that are not major manufacturing centers, the large-scale factories are generally located in, or near, urban areas.
The wage compensation by region varies dramatically. The average annual compensation (a proxy for hourly wages) across all regions for larger manufacturers was 18,000 yuan, versus almost 32,000 yuan in the Beijing area – a difference of more than 70%. The Shanghai region is also comparatively expensive, at an average of just over 30,000 yuan annually.
These wage discrepancies have caused some Western manufacturers to move production further inland, away from the higher cost coastal areas, but there are trade-offs.
“Leaving places with higher labor compensation costs may bring negatives such as more inconvenience, higher costs of transport and logistics, greater bureaucratic logjams, and shortages of experienced and educated and talented employees,” the report notes. Stronger logistics support and the availability of component suppliers nearby can make the higher labor cost areas still the best choice in terms of total supply chain costs.
But such moves are tempting. Economist magazine says companies can save a third in power costs and half in wage bills just by relocating a factory half an hour’s drive outside of Guangdong’s capital city of Guangzhou.
Continued Upward Pressure
As SCDigest has noted before, rapid economic growth has led to significant upward wage pressures in most of China. Wages on average doubled from 1998 through the 2004 census period, and have had strong gains by most estimates over the past few years as well. Wages for larger manufacturers are growing especially fast, fueled in part by rapid productivity gains in factory operations.
“Rising labor compensation in China has begun to erode the country’s manufacturing price advantage,” the report says.
As a result, for basic, labor-intensive industries, other low-cost countries (LCCs) such as India, Pakistan, and Vietnam are becoming more attractive. Meanwhile, China continues to move upstream in terms of the sophistication of the products it can manufacture and increasingly design and engineer.
The full report provides a wealth of additional data that can help companies better understand what is really happening in terms of China’s labor costs.
Is there anything in this report summary that surprises you, or that is different than your experience in China? Do you think upward wage pressure will drive companies to other LCCs? Let us know your thoughts at the Feedback button below. |