March
23, 2004 |
 |
 |
 |
 |
 |
  |
 |
 |
|
|
 |
 |
 |
 |
SupplyChainDigest's
Quality Web Seminars
Insight and Education
UPCOMING
EVENT:
DATE: |
Wednesday,
April 14
|
TIME: |
10:30
AM CT |
Featuring:
Tom Zosel Associates, McKesson Drugs,
and
Dana Corp.
Moderated
by SCDigest Editor Dan Gilmore
Click Here for More
Detailed Information and Register Today!
|
 |
 |
|
 |
|
 |
SupplyChainDigest’s
Archived Web Seminars
The
"No Spin Zone" -
only
from SCDigest!
Did
You Miss the Live Events?
Download
Your
"Pay-Per-View"
Archived Recording Today!
|
|
|
 |
 |
|
|
|
 |
 |
  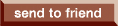 |
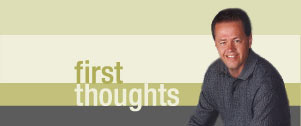 |
 |
|
Dan Gilmore
Editor-in-Chief |
 |
 |
 |
We
received much feedback two weeks ago when we noted the
many parallels between the emerging requirements for
RFID tagging from Wal-Mart, Target, the DoD, etc., and
the first waves of retailer compliance for UCC-128 container
labeling/ Advance Ship Notices in the early and mid-1990s.
Click here for an archive
of that article.
As
promised, it makes sense to review those initiatives
to consider any lessons learned and to make some guesses
about how things will play out this time. Here's my
view.
1. |
It will take longer than anyone thinks
: I remember trooping up to Troy, Michigan
in 1992 with Rick Baron, now of Alien Technologies,
for some of the early Kmart compliance meetings.
There, groups of about 25 dazed vendors heard
they had to start meeting the new labeling and
EDI requirements in something like four months.
Many of them weren't really doing anything four
YEARS later. Worse was going to the Kmart DCs
and seeing they weren't even using the technology
they were forcing suppliers to deploy at great
cost - except to levy fines for non-compliance.
This
will be a multi-year program for both retailers
and suppliers, though I think Wal-Mart is much
more organized to ultimately take advantage of
the tagging than were retailers in the first wave,
and I still expect schedules and usage dates to
slip. One wild card this time: RFID has for whatever
reason captured the interests of retail and consumer
goods company execs much more than bar codes ever
did, which may propel adoption. Also, the really
hard part of the first wave was EDI - and suppliers
can largely leverage that infrastructure to communicate
tag data.
|
2. |
Compliance
will be a back-end value-added service exercise
: Facing UCC-128 requirements, many technology
vendors and some retail suppliers looked hard
for an internal ROI to accelerate adoption. It
wasn't to be found, at least not directly. So
depending on order mix and operating procedures,
retail suppliers found ways to apply labels/collect
data either during the picking process, or as
a back end function on the way out the door. In
most cases, due to cost or timing, compliance
was enabled by "bolt-on" applications that connected
to whatever systems the suppliers already had
in place.
We'll
see the same thing here, as my conversations with
retail and technology suppliers support. Retail
suppliers looking for ROI from RFID compliance
are simply barking up the wrong tree. However,
UCC-128 compliance did in many cases act ultimately
as a catalyst to drive new capabilities that provided
ROI, especially in the order picking/WMS area.
But that took time - several years after compliance.
We'll see eventual adoption of fully-RFID powered
WMS systems too, but well after compliance requirements
are met.
|
3. |
There
will be three categories of retail suppliers :
These are: (1) aggressive early adopters (15%) who
believe this is an opportunity to improve their
position with retail customers; (2) cautious adopters
(60%) who want to comply and be a good partner but
don't feel urgency to do so any earlier than needed;
(3) laggards (25%) who either are just not well-organized
or view this as such a one-sided cost/burden that
they will delay until the last possible minute,
or until the fines for non-compliance become overly
burdensome. |
There's
a lot more we could say, but to repeat from last week
there is a very strong "déjà vu" feeling
about this whole thing for many of us.
Do
you agree with our parallels between the UCC-128 and
RFID compliance waves? Are companies looking for ROI
from RFID compliance going to find it? Is there advantage
to being an "aggressive adopter" company for compliance?
Let
us know your thoughts.
|
 |
|
|
|
 |
|
 |
This
Week:
Wow!
Forrester Report Says We Won't be Close to Five-Cent
RFID Tags for a Long, Long Time
New
Grocery Manufacturers Association Report Says
Data Synchronization Key to ECP/RFID Results
Are
We Finally Ready to Automate Purchase to Pay?
Summary and comment below.
|
|
|
|
Supply
Chain Investment News
Logistics software, 3PL and transportation
stocks had another rough week, as only
FedEx and Prologis found positive territory, up
5% and 4% respectively.
|
|
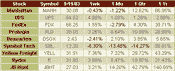
|
|
Click
here to see performance over the past week, month,
quarter and year >> |
|
|
|
It was also a rough week for Supply Chain
stocks, as the majority of the companies in
our index fell. Only SAP, Logility and
Aspentech managed to post (small) gains.
|
|
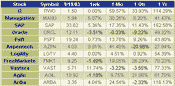 |
|
Click
here to see performance over the past week, month,
quarter and year >> |
|
|
 |
|
 |
Earlier
this month saw the release of the first ever TSI.
What is the TSI (it's logistics related, of course)?
Answer below
|
|
|
 |
|
 |
Reader
feedback from the topics in SupplyChainDigest
is growing every week! Keep the comments coming!
If you would like to keep your identity or company
anonymous, please let us know in your response.
Well,
we had a huge amount of letters on our First Thoughts
column two weeks ago on "A Big Price for Doing
Business in China" - on the increased pressure
from China on U.S. and European companies to turn
over intellectual property for access to Chinese
markets. We had way more responses than we can
print this week, but included as many as we can,
including our Feedback of the Week from Al Will
of the U.S Marine Corps.
For
more complete comments from readers, click
here.
Keep the dialog going!
Give us your thoughts on this week’s logistics
topics at feedback@scdigest.com.
|
 |
 |
|
|
|
|
|
 |
View
full article>>
For
some time now, starting with the work of the Auto ID
Center, there has been talk about the mythical five-cent
RFID tag, a price level at which supposedly ROI would
begin to show up with ease. The Center's comparatively
simple chip specification was designed to enable low
cost tag production and sale somewhere in this range.
There
has always been a bit of fuzziness to this whole discussion
- it was never quite clear at what unit level the five-cent
tag would drive usage - it's patently absurd in my opinion
for RFID to work at the item level for non-luxury goods
until it's basically free, like a current UPC code,
"printed" as part of the packaging.
Now
comes a new report from Forrester Research that predicts
tags will only reach 26 cents each by 2012. The study
comes from Forrester's European office, and the costs
are actually in euros, but it's close enough to U.S.
dollars for the discussion to be the same.
Forrester
based the prediction on interviews with a large number
of chip-related manufacturers, combined with analysis
of the fundamentals of chip design and production. The
two key factors behind the conservative view of price
decreases include:
|
Tag
assembly (connecting chips to antennas) currently
represents about 35% of tag production costs.
There is no clear path to reducing these assembly
costs, providing a pricing floor well above five-cents.
Forrester notes firms like Alien are trying to
develop new manufacturing processes that can break
this barrier, but says there is not enough evidence
these new techniques are likely to succeed. |
|
Volumes will take
longer to scale than many think, as the tag prices
themselves, slowness in retailers and others moving
to large scale production systems from initial pilots,
and the reality that many different tag types will
be needed even within the EPC framework, limits
the pace of volume-based price decreases. |
This
is fresh news, and I haven't heard any reaction yet
from tag manufacturers or retailers challenging the
prediction.
Key
Takeaway: I don't think anyone knows what's
real in terms of how fast tag prices will - or will
not - fall, but this report highlights the significant
ambiguity behind the holy grail of the five-cent tag.
Companies, especially those that may have to put tags
on millions of cartons, should do some scenario planning
around many different price-volume curves.
Do you think the Forrester analysis
is likely to be accurate, or is it way too pessimistic?
Will a failure to create the five-cent tag any time soon
really slow down the RFID/EPC movement? Let us know your
thoughts.
|
  |
 |
 |
Another
good report ("Connect the Dots") from the Grocery Manufacturers
Association (GMA) along with the Food Marketing Institute
(FMI) and National Association of Chain Drug Stores
(NACDS), focused on the need for improved data synchronization
between retailers and consumer goods manufacturers to
enable supply chain collaboration and maximize the potential
of RFID.
The
full report is available at the above link, based on
surveys with 80 or so manufacturers and retailers. Here
are the highlights:
|
The
report concludes that most companies agree for
the need for a single, global data registry (i.e.,
UCCNet), though no specific data is provided to
support that claim. Huge percentages, however,
of both retailers (100% of respondents) and manufacturers
(71%) are planning advanced data synchronization
efforts. |
|
While many companies
have signed on as UCCNet participants, less than
1% of global retail sales currently involve registered
and synchronized products. Manufacturers cited the
need for internal data cleansing efforts (46%) as
the largest barrier to increased participation. |
|
Manufacturers
overwhelmingly viewed improved inventory management
and supply chain visibility as likely benefits of
RFID/EPC, while a somewhat lower percentage of retailers
agreed. Most retailers, not surprisingly, were more
interested in out-of-stock avoidance. |
|
Interestingly,
retailers were much more concerned with EPC standards
being completed to spur adoption than were manufacturers. |
|
76% of manufacturers
and 66% of retailers believe that data synchronization
always or potentially should precede EPC adoption.
|
The
report is interesting, though seems to have been designed
from the start to support a point of view. The statement
is made that "without GDS [Global Data Synchronization],
EPC technology represents nothing more than an expensive
bar code."
Key
Takeaway: The link between RFID/EPC and data
synchronization has not been given enough attention,
and is confusing given the potential overlap between
UCCNet and the potential Object Naming Service (ONS)
servers in the sky. The whole industry does need to
"connect the dots" on this one.
Is data synchronization the key to
EPC? Do we need that in place before EPC delivers value?
Is the role of UCCNet and ONS clear? Let us know your
thoughts.
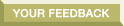 |
  |
 |
 |
View
full article>>
According to
a recent study by the Hackett Group, a very high percentage
of companies are putting heavy focus on streamlining
"procure to pay" processes, hoping to reduce cycle times,
overhead costs and the costs of purchased goods themselves.
The authors believe
that to really drive improvements, companies need to
do more than tinker at the edges of basic process re-engineering
within the purchasing department - real results occur
when the entire process is reviewed and improved across
multiple functions. Especially key is great integration
of purchasing and accounts payable processes - Hackett
notes one example of where the A/P department was actually
moved into the purchasing group at one large company.
The article notes
that there are many benefits resulting from a more comprehensive
process redesign, including:
|
Improved
root-cause error resolution, especially reducing
errors in payables resulting from PO discrepancies.
|
|
Improved goal
alignment/attainment: Cross-functional design can
get goals and metrics on the same page. |
|
Improved opportunities
for overall improvement: Results from expanded scope
and potential synergies across functions. For example,
"in the purchase-to-pay process, implementing a
new paperless process with electronic purchase orders
on the front end and electronic invoices or evaluated
receipt settlement (ERS) on the payment side is
considerably more effective than doing one without
the other." |
Nonetheless,
their research finds only 14.5% of companies manage
procure-to-pay as a single, integrated process.
Key Takeaway
: Too many of us thought "e-procurement" technology
was the key to improve purchasing processes. It can
play a vital role in that improvement, but with a total
process this complex, it's clear a more holistic view
is needed to really wring out efficiencies. Success,
however, does not require that all the functional groups
involved report to one individual - but the CEO does
need to appoint one process owner with the clout and
skill to herd this group of cats across the corporation.
Has your company
looked holistically at procure-to-pay processes? What
were the results? Can major improvements across the
entire process be achieved while traditional functional
groups and reporting are maintained? Let us know your
thoughts.
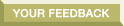
|
  |
 |
|
|
|
|
 |
I just read your
article on China's practice of forcing companies to
share technology as part of the "sales package".
I am glad to see your publication and others bringing
this problem to light. Some U.S. companies are utilizing
a short-sighted approach to business when they share
their technologies with the Chinese. It may provide
quick sales for a near term increase in income on the
balance sheet but it bleeds our country of R&D,
which is paid for with money and man hours. Leading
edge technology keeps our economy strong. My father's
company noted this trend in the Chinese back in the
70's when they tried to open a dialog with a firm from
Beijing that was a potential customer. As a member of
the U.S. military I also have concerns that this technology
sharing will shorten their timelines for producing hi
tech equipment that supports their military. That could
be a serious issue for us in 20 years.
Please continue
to include articles on this in future issues.
Lt.
Colonel Al Will
U.S.
Marine Corps
|
  |
 |
 |
Yes,
my company has definitely been affected by offshoring
to China. Our biggest customer, Home Depot, has
dropped their contract with my company, Werner Co.,
and started doing business in China. This, in
turn, has reduced our business so much that we are shutting
down our division at the end of this year.
Approximately 750 people are being affected by this
shut down. My company has also opened a new plant
in Mexico, which will take the place of the one I'm
employed with. This has been a disappointment
and will be a struggle for several associates as we
try to find gainful employment in the future.
Name
withheld

Somewhat scary
proposition as we feel the immediate pain from job loss
off-shoring, much the same as with Japan after WWII,
as you stated in the article. However, in the
long run, the U.S. is stronger, more industrious, more
ingenious, more productive, more competitive, and produces
higher quality products as a result of free-trade markets.
Don't you think we are simply repeating this process
again, and with a larger potential economic impact due
to China's size? I also believe that China will
be successful in obtaining the high technology "secrets,"
whether we share them willingly or not, and only a matter
of time. We must continue our quest in the U.S.
to stay ahead of the technology and innovation curve;
that is our true competitive advantage in this world
economy.
Jon
Walsh
VMG
Consulting
There is a
new term being used to describe the change from a manufacturing-based
to a service-based economy - "Creative Economy".
This concept predicts a US society where the only manufacturing
is research and development or emerging technology.
The problem with this concept is getting the majority
of the US workers to have the skills or desire to perform these
new "Creative" jobs. It has been the availability
of good paying jobs in the manufacturing sector that
has allowed the average American to achieve a standard
of living envied around the world.
Another fundamental
flaw with this "Creative Economy" is the assumption
that American workers would be involved with research
and development for the next generation of products.
Historically, the companies that manufacture the products
lead the R&D effort and unless our "Creative"
services are less costly than our competition's, it
is unlikely we would see the work.
Manufacturing
has always been the hallmark for the most highly developed
countries. The industrialized nations have always purchased
raw materials and cheap services from third world nations.
Is that really the direction we want to head?
As an Economics
major I too believe in free trade, however, unregulated
free trade presumes a free market that is fair and balanced
by unregulated economic pressures. That condition does
not exist in our Global economy.
Companies have
to start taking a longer view in their planning process
to determine what has to be done to keep manufacturing
in the US.
Herb
Minor
First, an emotional
reaction. This story comes on the heels of widely
documented abuses of American intellectual property
such as software and movies. Counterfeit copies
of Microsoft products and current release movies being
sold on Chinese street corners with no apparent enforcement
of international copyright law by the Chinese officials.
The Chinese have no regard for us or our property and
I am very disturbed by their latest moves to demand
that property be turned over on the condition of doing
business in their country. What an arrogant group
of people!
Second, I have
seen a similar situation before. About 15-20 years
ago I was working in the aerospace industry for a manufacturer
of aircraft equipment. A large, American aircraft
OEM was anxious to sell planes to the Japanese and forced
all of their key suppliers to acquiesce to a deal that,
I'm sure, many of the suppliers would rather not have
agreed to. The Japanese purchased the aircraft
that used equipment built by my company. As a
condition of the purchase, the Japanese buyers demanded
all intellectual property to support the design, manufacture
and repair of said equipment. They also demanded
that their service technicians be provided full access
to the manufacturing and rebuild process when their
equipment passed through our shop. They asked
an endless stream of questions and were never satisfied
with the details provided. They always wanted
more and waved the technical license agreement whenever
we tried to explain that there was nothing more to share.
Eventually, they
stopped buying parts and services for the equipment.
Their strategy all along was to become self sufficient
in the manufacture and repair of the components. No
telling where that technology ended up and how it benefited
the economic advantage of Japanese companies.
The total sales gained by our company over the short
term had to be small relative to the long-term benefits
that the Japanese gained. To this day, I question
why anyone would negotiate a deal like that.
Denis
M. Wolowiecki
Accenture

I think it is
ridiculous that those companies continue to do business
over in China. It just shows what American companies
will do to help the bottom line. I am afraid that eventually,
we will loose all major manufacturing and services to
countries like China and India. When that happens, the
United States will no longer be a leader in the world
and could possibly be looked down upon as a third-world
country.
Mike
Dewey
Heraeus
Kulzer, Inc.

A good editorial
regarding offshoring and intellectual property.
But let's face it, this is not new. We have been
seeing excellent copies of all kinds of machinery goods
(and other goods) from China for decades. I saw
Chinese copies of Bridgeport verticle mills 20 years
ago. And I know a division of the company I used
to work for that set up operations in China only to
eventually find that the exact equipment they had previously
"joint ventured" became the sole venture of
their former partners.
What are you
going to do? Sue? Then what? Collect?
All companies
should be wary of this huge market. The temptation
is great but the rewards are temporary, and then potentially
damaging. The problem is always the same.
If one company stands up and says no, another company
says yes, and gets the contract. The issue is
the same for all outsourcing. Anyone who says
no is the one at a disadvantage today. And tomorrow
is shaped by those who say yes.
This is exactly
why we as a nation have the power to regulate commerce.
Until we strictly review outsourcing in terms of technology
and job exportation and its future impact, the market
will force us towards the maximum. The consequences
are astounding and people are just now waking up to
it. But unfortunately, the "R" word,
Regulation, is seen as such an abomination by business
today that they could never admit its necessity.
It will be our downfall.
Phil Gilmore
Extendible Conveyors |
  |
|
|
|
|
 |
Q. |
Earlier this month saw the
release of the first ever TSI. What is the TSI?
|
A. |
TSI
is the Transportation Services Index, a new monthly
measure of U.S. economic activity based on transportation
data, from the Department of Transportation. The
TSI combines data from both freight movements
(rail, air, water, truck, pipelines) and commercial
passenger travel. The new index is computed based
on data going back to 1990.
|
|
  |
 |
|
|
|