Once again, maybe I should reconsider taking a few days off each year.
In the almost 10 years of Supply Chain Digest, writing something like 48 columns a year, I have only missed the call on 5-6 occasions, giving up the prestigious First Thoughts platform to a small group of guest commentators.
Gilmore Says: |
I learned a long time ago that some people can think at a system level, and some simply cannot. Hopefully, those rising up the supply chain ranks are capable of doing so, but I suspect that is not always the case.
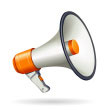
Click Here to See
Reader Feedback |
For each of the past three summers, one of those guests has been David Schneider, a former retail industry logistics executive among many other accomplishments, now running his own consulting firm. This year, I coaxed a two-part series out of him, on "systems thinking" - or more accurately, the lack thereof - in the supply chain. You'll find those column here: Systems Thinking Part 1 and Part 2.
Well I'll be darned if those columns didn't generate more reader feedback than I have had in any of my columns for quite a few months. While modestly upset with that fact, I am happy it has been enough that I can do a "Reader's Respond" column this week for the first time in awhile, presenting the highlights of the 20+ emails we received, making it an easy week on me.
So here we go.
John Mayo of GE was one of the first to respond, saying that "I think most companies use some form of systems thinking for supply chain systems. It is the degree to which they apply and use technology advances in their design that is the bigger issue."
I agree - but I believe that for reasons I will explain later that systems thinking is in fact often quite limited.
Mayo added "That said, many companies could improve the business and system processes within their four walls with a strategic view of how to improve the key drivers of the supply chain. From my own experience, it still seems likes there are too many hands in the pot, and not enough ‘intelligence’ in our systems."
Trevor Miles of supply chain software vendor Kinaxis sent in a great letter on the topic, in part saying that a downside to some systems thinking is that it created a belief that a full a supply chain system can actually be accurately modeled in software and optimization engines.
"There are so many nuances and competing objectives in a decision that change frequently that I do not believe we can write an objective function for an optimization that captures all the trade-offs that need to be performed," Miles said. "How does one translate customer service objectives, inventory levels, revenue, and margin into a common UOM against which we can run an optimization engine? And all that assuming we know all the variables with sufficient certainty that the optimum is meaningful. Well, we don’t."
That is a very interesting perspective that we will explore in more detail on these pages soon.
My good friend Gene Tyndall of Tompkins International as usual offered some supply chain insight on the topic with these comments:
"Systems thinking, when applied to supply chains, addresses the four supply chain flows: physical, information, cash, and work," Tyndall observed. "Supply chain managers often lose sight of this fact - that supply chains are really about the efficiency and effectiveness of how these four flows perform. Every incremental change we make in any supply chain processes is only as important as its effects on one or more of these flows."
He added that "The "age of specialization" has been beneficial for the most part, but has help create siloed thinking when systems analysis was overlooked. We need to get back to a balance of both."
Schneider had a bit of a distribution center orientation in his pieces, and I completely agree his example of a clear lack of systems thinking in most operations is the DC receiving process. Watch the process for awhile, Schneider said. Does it look like it was optimally designed across shipper, carrier and receiving company? Hardly.
So, Chuck Crews of Fruit-of-the-Loom wrote us that "This [article] is excellent. Whether or not DC management (as an example group) utilizes system thinking or not can make or break a distribution facility. I've seen it as you have (both positive and negative)."
Along the same lines, Mark Fralick of GetUsROI has noted for years that distribution center excellence is in the end all about "flow," and to optimize total flow across a full facility obviously requires a full systems perspective - and supporting technology that can execute that vision.
However, Fralick notes there are some natural barriers to the systems thinking approach.
"The problem I see is that there is rarely one perso who is responsible for all of this. You have elements of marketing forecasting, purchasing, transportation, distribution, etc., involved," Fralick notes. "In the real world one of the big reasons that people don't think this way is that there are a lot of fiefdoms in play and no one is sharing their time and effort to look at the big picture. If you get these various hats all in the same room together periodically and just communicate - that is the key."
Shelley Jordan of NobCessory agrees with Schneider and wrote that "I believe it is difficult for most to master the systems thinking approach and not just think and use causal diagrams, but implement solutions."
Causal diagrams are essential to effective systems thinking, Schneider said, and Jordan agreed, saying that "We are creating casual diagrams regularly and they change our decision making process."
Maybe you should be employing causal diagrams too.
Millard Humphreys of QED Logistics says that like Schneider he has used a systems thinking approach with success for years.
"The causal diagram and some of the Lean-Six Sigma tools are indeed keys to implementing systems thinking," Humphries said. "Two additional requirements are that an individual be prepared to perform a thorough analysis without leaping quickly to what may be erroneous conclusions, and second that the individual/team have full understanding of the process, including those areas directly impacted and those only tangentially related."
He added that "It is this latter requirement that makes systems thinking a particularly suitable tool for supply chain processes, as supply chain impacts most if not all of the various functions and silos within an organization."
There were a number of more emails, but unfortunately we are about out of space. We'll publish the rest in our Feedback section below over the next couple of weeks.
My own view: I learned a long time ago that some people can think at a system level, and some simply cannot. Hopefully, those rising up the supply chain ranks are capable of doing so, but I suspect that is not always the case.
That said, a systems approach almost by definition has a cross-functional impact. That makes it hard - and is why so many decisions and processes are in fact relegated to silos.
It takes very strong supply chain leadership to break through those silos and consistently adopt a systems approach. If that leadership is missing, systems thinking will nevertheless come eventually as part of a supply chain transformation -usually with a new head of supply chain in charge of the effort.
Any reaction to these reader comments on systems thinking? We would love some more. Let us know your thoughts at the Feedback section
below.
|