There are obviously dozens of supply chain technologies out there to consider, and I can by no means claim to be expert in all of them, but think I know my way around most of them more than the average bear.
So, reprising an effort I first did in 2007, with some updates/additions/changes, I am going to list 10 technologies to consider for supply chain and logistics improvement based on a "pain to gain" ratio analysis. That is, if implemented well, let's assume that some benefit will be realized by each any given technology area (otherwise, what's the point?). But the potential benefits differ across technologies.
Gilmore Says: |
Ok, so here it starts to get interesting, as Inventory Optimization software can offer significant improvement in inventory effectiveness, but usually with a decent amount of pain to get there.
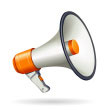
Click Here to See
Reader Feedback
|
These technologies also tend to have different "pain" levels associated with getting them deployed. Some are simply harder or more expensive to implement than others. So, a "pain to gain" ratio it seems to me is a reasonable way to think about things, especially as pain also relates to implementation risk.
While it may be true that there is a "no pain, no gain" principle in areas like fitness and education, in business finding the least pain for the most gain seems to me to be a smart way to operate.
So that said, below is my list of technology attractiveness based on some relationship between pain and gain. Of course, I could add all sorts of caveats relative to any individual company's current situation, skill sets, maturity, etc., but I assume that is understood by our readers here.
Scores for pain and gain are out of a maximmum score of 5.
1. Labor Management Systems (LMS) in Distribution: While not the most exciting technology in the landscape, Labor Management simply delivers time and time again. A combination of software, engineering and mindset change to improve logistics productivity, Labor Management Systems are typically built on discrete, engineered standards for specific tasks in a distribution center, plus detailed reporting at the individual operator level against the resulting dynamic goal time calculations for the day’s work. Very little pain and risk, with labor savings of 10-20% or more, which are substantial and very consistent across companies. If these benefits are not achieved, it is almost always an implementation issue. Pain: ** Gain: $$$$. One of the first things I would do in any decent size DC operation. It is number 1 because of how consistently the expected results are achieved.
2. Demand Planning Software: I know most decent size companies have already deployed an advanced demand planning tool, but nevertheless I keep running in to businesses that haven't. Any pain involved usualy has little to do with the technology itself, but rather the effort associated with developing the capabilities required to effectively use the tools and change processes. In that sense, there is very little business risk, as companies should always be able to revert to previous methods if they run into trouble. The improvements from statistical forecasting are often highlighted, but the ability of these tools to enforce process discipline is often of equal or more value. Pain: ** Gain: $$$$.
3. Spend Management Visibility: Another software that has been highly adopted, nevertheless many still firms are still outside looking in. These tools provides greatly improved visibility to what a company actually spends, where, with what vendors and more. Amazing insight is thus revealed. The pain primarily around systems integration - and perhaps mentally with all the silly things companies find they are doing in buying stuff. Pain: ***. Gain: $$$$$. It works at home, doesn't it - why not in business.
4. E-Auctions Tools: Use of technology tools to empower on-line contract bidding for a growing array of both indirect and indirect materials is also well penetrated, but far from universal. Once viewed as a cure-all, there has lately been some realization that there are limits to how far this can/should be taken (though not all feel this way). Increasingly being used for services procurement as well as products. Direct materials are harder than indirect, but many do both. Fighting entrenched procurement methods may be the largest barrier to deployment success. Reports of 15-25% savings for first events in a category are common. Pain: **. Gain: $$$$.
5. Supplier Portals: The technology has existed for some time now to relatively easily integrate suppliers through increasingly functional web portals. The scope of potential activities is very broad, from purchase order management, to providing demand visibility, to advance ship notice and bar code label generation, to generating dynamic inbound shipment requirements depending on needs and industry. The technology here just keeps getting better. The opportunity to connect suppliers that aren't EDI capable is clear. Pain: **. Gain: $$$$. What would be the reason for any large company not to do this?
6. Wearable Wireless Terminals + Voice in Distribution: Amazingly, in a sense, it is becoming clear to me that for order pickers and some others in the distribution center, there is a technology combination that objectively offers the most productivity and flexibility. That is to use "wearable" wireless terminals worn on the forearm in combination with voice technology. The wearable units also enable "hands-free" operation as does pure voice, but offers other functionalities. So, voice sends the next location to the pickers, the accuracy of which is confirmed via bar code scan. Expect picking costs, usually the highest single cost component in the DC, to drop 15-25%. About the only real pain is spending money for the new gear. Pain: *. Gain: $$$.
7. Modeling the Supply Chain: This can be short-hand for "continuous network optimization," but a number of companies (e.g., Schneider National, Lowes) have done this on their own without using commercial network optimization tools. Regardless of approach, it means developing a model of how the supply chain works in terms of cost and service, which can be used for scenario planning and for decision support on a continuous basis. While traditional network optimization focuses on the "big picture," this involves help for the many decisions about production, product flows, make versus buy and many other tactical areas, not the network as a whole. The pain is obviously around setting up the model (hardly trivial) and keeping some staff focused on the effort. The savings, however, can be millions annually for large/complex networks. Pain: ***. Gain: $$$$$.
8. Transportation Management Systems (TMS): This is hard to address in a sense, in that TMS means different things to different companies, and goals range from basic execution automation to comprehensive "transportation transformation," but nevertheless, overall, TMS still offers great value proposition for most. The pain and the gain vary directly with the scope of the deployment, and "on-demand" TMS adds a new twist. Regardless, the dollars that can be added to the bottom line from TMS is significant, and TMS also impacts customer service in a big way. Pain: **. Gain: $$$$. How can you really operate a supply chain well without an effective TMS? Though TMS can be had through outsourcing.
9. Inventory Optimization: Ok, so here it starts to get interesting, as Inventory Optimization software can offer significant improvement in inventory effectiveness, but usually with a decent amount of pain to get there. Why the pain? Because it upsets the apple cart in terms of how inventory is managed, and forces company to rethink metrics, responsibilities and other aspects of its supply chain, as inventory targets are set holistically across tiers and nodes. The gain? Inventory reductions of up to 30% (I have talked to companies that have achieved that), and increased revenue growth from reduced stock outs. One of the most intriguing applications out there. Pain:***. Gain $$$$$.
10. Data Quality/Master Data Management: I was tempted to put this higher, but left it here because it is as much journey as destination. The simple fact is that data quality issues have a huge impact on supply chain excellence, even though quantifying that impact is very difficult. But the evidence is clear that companies that tackle and conquer master data issues simply can't imagine going back. That means a big effort upfront, and on-going cost for continuous maintenance. Last I heard, GE still had dozens of staff in India doing nothing but enhancing master data. SABMiller found managing master data worked best in the supply chain organization, not through ERP. This is an important not urgent issue, which is why it often drops off the funding list. Too bad. Pain:***. Gain $$$$ (probably four and a half, though tough to measure).
So that's my list. I by no means am claiming this is a scientific analysis, just a representation of what I have seen and continue to see in terms of what is being achieved. Take it as one input, nothing else.
What is your reaction towards Gilmore's analysis of supply chain technologies and the "pain to gain" ratio? Let us know your thoughts at the Feedback button below.
|