Well, oil futures have recently "plummeted" to a mere $98 per barrel or so, a level that as I noted a couple of months ago that seemed like the end of the world less than five years ago. Now we complain but take it pretty much in stride.
Though some are predicting will reach $150 or so again before too long, and others citing even higher figures over the coming years, I am not so sure about that. First, in the US at least, $4.00 per gallon of gasoline does seem to be some sort of upward bound that leads to changing consumer behavior and thus demand destruction that acts as a counterbalance to upward pressures on price. Not sure if this is the same elsewhere - did you know, for example, that China significantly subsidizes gas prices for consumers and truckers?
Gilmore Says: |
Your potential strategies and "degrees of freedom" will vary significantly by type of cost driver. It is a worthwhile exercise to develop that matrix and discuss it internally.
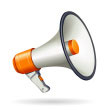
Click Here to See
Reader Feedback
|
I will also note that we are in this sort of terrible place where the most likely way we will drive oil prices back down is through a slowdown in the economy. So, if you want the lukewarm recovery to continue and maybe even expand, it has to be a the cost of higher oil prices. But higher oil prices cause the economy to contract.... my head hurts. I had one economics class as an undergrad, and one in grad school. Don't think I will drag out the textbooks to try to sort all that out.
All I do know is that transportation is a huge element of supply chain costs, representing 6% or so of US GDP and even higher level in many countries, that rising oil prices add significantly to the cost of moving goods, and capacity pressures are also coming into play.
So, what can shippers do about that? I amazed at the sophistication of supply chain professionals today, so most probably know all these ideas presented below and more, but perhaps it is handy to have them in one place anyways.
One useful framework for any supply chain challenge, but I think especially so for rising transport costs, is to identify all the drivers of transportation spend and divide them into three categories:
1. Things can you can directly control: For example, how full you load your trucks
2. Things that you can't control but can manage: For example, rate or surcharge increases from carriers
3. Things that you can't control but you can influence or mitigate: For example, you can't change the price of oil, but some companies can and do hedge the price of oil to lock in a given cost.
Your potential strategies and "degrees of freedom" in each category will vary significantly. It is a worthwhile exercise to develop that matrix and discuss it internally.
With that as an intro, here are some potential areas that can lead to reduced transportation spend:
Strategic:
• The trade-off between inventory and transportation cost is a constant exercise. While the push in recent years is to drive down inventories; maybe it is time to shift your position on the curve.
• Many networks were not built with $100+ oil in mind. I think it is here to stay - may be time to re-evaluate you network strategy. That's why having a network tool in place for continuous use can be so valuable.
• Invest in a TMS, if you haven't already done so, or change/upgrade if it is old. Savings from consolidation and mode/carrier optimization through TMS can be substantial. On-demand offerings mean low upfront investment and you can be live in just a few months, and even faster in some cases.
• If you haven't already, centralize transportation planning versus decisions at individual ship sites.
• Hedge the price of oil (though this would have been a lot smarter a year ago)
Tactical:
• Can changes to packaging be made to ship less air? For perhaps 98% of companies, the answer is yes - sometimes dramatically so. One cell phone distributor increased units on a pallet by 50% through a new package design effort. Where are you on the protection versus logistics costs curve?
• Ditto for carton sizes and utilization in pick-pack operations. My friend Jack Ampuja has convinced me optimizing this can drive big transport costs for most shippers.
• For those that have avoided rail/intermodal for various reasons, now may be the time to rethink that, or at least take another look.
• Consider taking over greater if not total control of inbound freight.
• Look for collaborative shipping opportunities; more and more companies are making arrangements with complementary shippers. But it takes work to find and develop them.
• See if it may make sense to sub-optimize manufacturing to reduce transportation costs, especially in terms of uneven load patterns that exceed carrier commitments and result in expensive spot market moves. One large soft drink distributor is doing exactly that.
• While you should be fair to carriers, most large companies now set fuel surcharge payment policies, rather than accepting a carrier's schedule.
Operational/Execution:
• Improve trailer loading through pallet and trailer cube optimization. My friend Thomas Moore has likewise convinced me there is a lot of improvement available there for most companies.
• Revisit TMS settings and assumptions. Are you limited to two-stop multi-stop routes, when maybe you could go for three, as an example?
• Evaluate how consistently the transportation plan is executed as planned. Many companies have yet to well tighten up the common planning-to-execution gap in transportation.
• If you have a routing guide, take steps to ensure internal shippers and external vendors are highly compliant.
• Reduce the number of "bad loads" that you are dispatching (e.g., poor capacity utilization). Many shippers just live with this. See if these loads can be held for a day to improve consolidation.
• Evaluate you level of expedited transportation and use root cause analysis to drop that level substantially.
• Send better forecasts to core carriers to improve chances they can have capacity to support your needs.
I am sure there are dozens of more ideas/opportunities, but these I think are some of the best. How about adding your thoughts to the mix?
Do you like or use the framework of controllable, manageable, and mitigate-able cost drivers? What other ideas would you add to Gilmore's list of freight cost savings ideas? Let us know your thoughts at the Feedback button below.
|