As you may remember, as part of my refresh of SCDigest's Supply Chain Megatrends list in 2012, the first two were related to: (1) A new era of "turbo" supply chain visibility; and (2) how that extreme visibility will drive something very close to "perfect logistics," because what can be seen can be controlled.
I have received many positive comments and a handful of negative ones regarding my concept of perfect logistics (probably too early for a "PL" acronym, I suppose), with the general theme of the critiques being "we can never reach perfection," "where there are people involved there will always be errors," etc.
Gilmore Says: |
It won't take the parcel carriers long to figure out it doesn't make sense to take a package to a consumer that is likely to be refused.
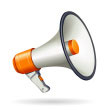
Click Here to See
Reader Feedback |
I accept all that of course, and probably could be talked into "almost perfect logistics" or something, except that doesn't sound as good, and I really believe in many areas we will in fact start to reach perfection, or darn close to it.
I had the chance to present on this topic at the Motorola Solutions reseller/VAR conference in Las Vegas a couple of weeks ago, an event the forced me to review my thinking a bit, and update the original ideas and examples I had with a few fresh ones, which I will also discuss here.
As you may know, item-level RFID in the retail apparel sector is moving along nicely, albeit somewhat quietly, with programs at American Apparel, Macy's, Walmart, and JC Penney (though the latter has screeched to something of a halt with its overall business woes, and it will be interesting to see what happens if JC Penney CEO Ron Johnson is shown the door, which seems practically inevitable to me right now). Many others retail programs are said to be in the works, notably Kohl's and Gap Stores.
While the retailers are pushing this largely for in-store reasons (accurate perpetual inventories, cycle counts in minutes rather than hours, etc.), a few smart manufacturers are figuring out that as long as they have to put RFID tags on the merchandise, they might as well use them internally tool (if anyone sees the parallel to how bar coding evolved in the 1990s, you get an A for the day).
Dean Frew, CEO of Xterprise, says his company has been putting split case "auditing" systems in a number of apparel vendors. To greatly simplify, the system knows what it is supposed to be in the box (they are items individually picked and packed, as is common for replenishment orders in the soft goods industry, and the cartons are usually destined for a specific retail store by way of a retailer DC), and that completed carton is then passed through an RFID reader array to compare what is there versus what is supposed to be.
Frew tells me most of these vendors found quite a surprise. The accuracy rates of those mixed cases are often not at the 99%+ plus level most had thought, but more like 98% - and that is a big difference. If you know how this works, few vendors or retailers if any check every case for accuracy. There is usually a selective audit at the vendor DC and maybe the receiving side, and if a large number of errors are found, there may be a more comprehensive check. In general, however, most cartons, 100% accurate or not, are shipped from the vendor to a retailer DC, where they are flowed right through to the outbound door with a truck going to the appropriate store.
Store personal do not check the carton contents to see if they match what is supposed to be in that box. They simply put the merchandise away, allowing the accuracy error right into the system because the inventory system is updated with what is supposed to be in the carton, not what actually is. That error can later cause out of stocks and other problems until the retailer finally adjusts the inventory after a cycle count (and we assume just writes the missing inventory off, probably labeling it shrinkage or something). And by the way, a manual, non-RFID cycle count process is likely to create as many errors as it fixes.
So back to the vendor, where the errors all started. With the RFID auditing process, 100% of the errors are caught before the carton is shipped, and 100% of those cartons are fixed. Carton content accuracy, and hopefully along with it ASN and labeling accuracy, becomes in fact perfect. And that will save retailers a lot of costs and reduce out-of-stocks, and ultimately help vendor sell-through at the store as well. Naturally, this will lead the vendors to push the process back up into the picking process itself, so there are no inaccurate boxes to fix.
Example 2: This is a little more theoretical, but we were struck a few weeks ago by the announcement of a new product called the DropTag, developed by a company called Cambridge Consultants. In great summary, a DropTag contains a sensor that records how an ecommerce package has been treated along its journey, with an associated smart phone app that allows the consumer or business to scan the tag when the delivery person shows up and see, for example, if the package has been dropped. (See Quest for Perfect Logistics Continues as New Chip Tracks Whether Box has Been Mishandled on Way from E-Tailer)
If yes, for certain categories of products (electronics, fragile items, etc., which are likely to be the only ones to receive a tag from the e-tailer to begin with), the consumer may decide to refuse the shipment and hand it back to the UPS or FedEx driver. The company says it also plans to later add a temperature sensor, which could tell a consumer whether the prescription from drugstore.com was exposed to high or freezing temperatures, for example.
I have no idea whether this idea will be attractive to e-tailers, or how the parcel companies would react to such a development. (For all I know, they may refuse to accept a package with a DropTag). But let's assume for the moment it does gain some traction.
Well it won't take the parcel carriers long to figure out it doesn't make sense to take a package to a consumer that is likely to be refused. So they will instead read the DropTags themselves along the way, and likely send the parcel back if its handling has exceeded whatever the standards are.
Of course, the carriers will then increasingly be able to determine the where, when and who of the excessive handling. That visibility will naturally lead them to adjust process, equipment and personnel as needed to significantly reduce the problems – getting us a lot closer to logistics perfection.
The DropTag itself may never see the light of day, but I hope you get the point. The array of visibility tools (bar code, RFID, wireless, video, GPS, sensors, etc.) continues to get cheaper, easier to deploy, and smarter, and I predict we will see increasing numbers of these kinds of examples such as the two I presented today. I mean, how long will it really be before we can eliminate the scourge of inaccurate pick-pack cartons, as some apparel vendors are already doing?
And if the apparel supply chain does it, won't it almost force other supply chains to go the same way? (Remember, cans of soup and such, where there would be a huge issue with tag costs, are rarely moved in less than full cases).
We may never actually reach the town of Perfect Logistics, but it doesn't matter. That's where the train is headed.
What are your thoughts on these two new examples of Perfect Logistics trends? Is there anything along these lines your company is doing or investigating? Let us know your thoughts at the Feedback button (email) or section (web form) below.
|