Ok, for the second week in a row I was on the road at a major trade event. Last week it was the NRF show in New York City, this week it was ProMat 2013 in Chicago, where I marched the aisles for two days with our Materials Handling Editor Cliff Holste.
For those that don't know ProMat, it is a bi-annual event from MHI (until recently the Material Handling Industry of America or MHIA), which as the name suggests focuses on materials handling systems and solutions, mostly for distribution but some manufacturing, plus related software solutions such as WMS. There are also dozens of vendors offering an array of products that I will just say are connected to distribution, plus the usual consultants and more, and you wind up with a large show of some 800 booths.
Gilmore Says: |
What was very hard to find was any emphasis on traditional batch picking plus downstream sortation systems that have been the mainstay of this industry for decades.
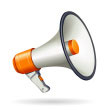
Click Here to See
Reader Feedback |
This year for the first time, MHI also partnered with the Industrial Robotics Association to offer the Automate show in an adjacent exhibit hall, which had a dizzying array of robotics, mostly for manufacturing.
As usual, we did video reviews for the first two days of this four-day show – you will find them here: Promat Day 1 and ProMat Day 2.
One mini-trend this year was that in general, a number of vendors moved a bit away from bringing actual systems to the show – which can cost them up to $250,000, depending on the size – and towards fancy animations and video, often on impressive flat screen displays. While that trend may not please some, the reality is that you can often actually understand what is happening in the system better through the animations/video, and the vendor can use this technique to display more systems than it can bringing actual hardware. I think it is inevitable this trend will continue.
Cliff and I kind of travelled the right side of the show on Day 1, and couldn't really identify any key themes. Two years ago, it was the "Euro Invasion" – the growing and successful entrance of a wide range of European-based vendors to the US market. Four years ago, it was "automated case picking."
Well, on Day 2, as we traversed the main trail of major material handling providers we found our theme, which was sort of a triad of three inter-related trends: (1) automated piece picking; (2) focused on e-commerce applications; (3) generally using some flavor of "goods to picker" technology.
Noteworthy, the vendor that helped really promulgate the goods to picker approach, Kiva Systems, was not at the show this year at all, versus its prominent display right up front in recent years. That less than 12 months after it was surprisingly acquired by Amazon.com and amid rumors, which Amazon has yet to address, that the little orange robots moving inventory to operators at pick stations would at least for now only be used internally for Amazon's dozens of DCs. While not definitive, the absence of Kiva from the show certainly adds credence to those rumors.
As Cliff and I discussed in our Day 2 review, when combining the automated piece picking with a reasonably strong automated case picking (ACP) presence, what was very hard to find was any emphasis on traditional batch picking plus downstream sortation systems that have been the mainstay of this industry for decades. Those systems will be around maybe forever, and still bring in the bulk of the revenue for many of the large providers, but there is a bit of a feeling that this is yesterday's technology, though the transition as always will be slow.
On to some of the systems and products we liked.
Dematic provides a good example of the main trend we cited, demonstrating (with real equipment) its improved "multi-shuttle" system – which can put away and extract cartons/totes in a sort of mini-load AS/RS fashion – which was then connected to its RapidPick solution for piece picking. In that scenario, the shuttles are delivered to a pick station, the operator makes and confirms the picks into say shipping cartons, and that shuttle moves on to another pick station or back to storage, while another shuttle arrives.
We liked the improvements in the second generation shuttles, which are faster, quieter, and have a more flexible set of "grabbers" (my word) to accommodate cartons of various widths. Notably, when the multi-shuttle system was released a few years ago, it was targeted primarily at manufacturing applications for say bringing parts to work cells. Now, with e-commerce madness and the addition of the RapidPick capabilities, the focus has clearly expanded.
Along the same lines but with a different approach was a company called OPEX, whose Perfect Pick system does not use shuttles but what it calls "iBots," which traverse the storage structures without any sort of crane or lift. The iBots move standard size trays, on which totes and cartons are placed (you could even just put products right on the tray if you wanted), which are then delivered to work stations for picking into shipping cartons. We liked the fact that you could add pick stations on platforms above the ground level or on the other side of the tunnel. Also had clear path for inventory replenishment, one of the real challenges of these approaches.
There were several others along the same lines. While on the surface many look the same, there are differences – you have to really get into the details.
Of course, not everyone will want to automate the piece picking process at this level. For those, Intelligrated was demonstrating a new version of its "GoKart" mobile picking system. The innovation here is a flexible "pick-to-light" display that can adjust its light array depending on how many carton are on a shelf. Change from say three pick cartons to five, and the display makes the adjustment. It also smartly has a side area and light display just for single line orders. Nice product. Company says it sold 10 miles worth of these displays in 2012 – and they are just three-feet long.
Another approach to the e-fullfillment challenge came from a company called Accutech. The firm has been around for more than 10 years, but was making its first trip to ProMat. Accutech offers to solutions for automating the packing/bagging process: one where the operator puts the product in the bag, and the system then prints and adds the invoice or other material, seals the bag, then prints and applies the shipping label.
In the more automated system, product is placed on a conveyor, and the systems merges the product(s) with up to five items (invoice, catalog, promotional material), places them all in the bag, seals it, applies the label, etc. One of the key benefits of this more automated approach is that this system uses just rolls of polymer, not finished bags, creating the bags on the fly. The rolls of polymer are much cheaper than finished bags, and the bags are cut to the size of the items only. Company cited LL Bean, Cabello's and Pac Sunwear as customers.
A reasonable segue from that is to Systems Logistics, which makes a very wide array of systems (including automated case picking), but what we liked this year was the US introduction of its "Free Box" solution, which creates boxes on-demand in a DC or factory. In just 320 square feet, the system takes raw sheets of corrugate (much cheaper than finished boxes), builds the bottom of the box on one side, the sides of the box in another, then marries them together to create the finished box. Ink jet printers print bar codes and human readable information.
Based on the order or product details, the system can build the box as little as just one millimeter taller than the goods to be placed inside. The savings come from several areas: labor reduction in building boxes, reduced corrugate expense, and reduced shipping charges based on the more precise boxes. It's cool.
I am out of space, but all this and more are covered in the videos, with visuals. Next week, we will have broken down those full videos into individual clips by solution. In very brief fashion, we also liked the new "TECSYS Smart" solution from TECSYS that helps companies get more out of their WMS over time, Softeon's voice enablement of standard smart phones to connect supervisors and managers to the WMS in a DC, the truly innovative and "green" solutions from a company called Make-em-Move to keep critters and birds away from your products and facilities (you have to see them!), and the Warehouse Navigation system from Jungheinrich that improves the productivity of VNA trucks by as much as 25% by taking over control of their movement from human operators.
It was a good week. We could have easily stayed another day.
Any reaction to Gilmore's ProMat trip report? What did you see as interesting solutions there? Let us know your thoughts at the Feedback button (email) or section below.
|