It's the day before the Labor Day weekend here in the US and in Canada, and on this same day last year for the first time I wrote a column on The Labor (Day) Supply Chain. It went over pretty well, so I am going to repeat the effort here in 2012.
There may be some duplication, but heck I forgot most of what I wrote, so a little refresher can't hurt.
It is a coincidence - but very relevant - that just a couple of weeks ago, a strike by workers at a Caterpillar hydraulics systems plant in Joliet, IL that some had called "Labor's Last Stand" finally ended.
Gilmore Says: |
Less union-oriented right to work states in the South and Southwest have absolutely dominated major new factory announcements in recent years.
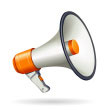
Click Here to See
Reader Feedback |
For some, the action by 780 or so workers represented at the factory by the International Association of Machinists and Aerospace workers was a seminal moment in the US labor balance of power. Union workers in manufacturing had been on the downside of the battle for many years, buffeted by the recession and high unemployment (which reduced their leverage), the constant threat of outsourcing, and the general need for companies to compete in a fierce global economy.
Here, workers weren't looking for increases – they were trying to push back, against a company known for taking a pretty tough stance with labor, on a series of concessions from the last contract relative to wage rates, health care contributions and more. This was in the context of a company that all told is doing well and is highly profitable – but one that also has opened several non-unions factories in the south in recent years.
The strike had been going on since May 1.
In recent weeks, the toll of just $150 per week strike pay was too much for some, and a little over 100 were said to have gone back to work. The plant was able to keep production rates at a decent level through supervisors and temporary workers manning the lines.
In the end, what happened was really not unexpected: the union accepted, by a very slim margin, a contract largely similar to what was offered originally by Cat and overwhelmingly defeated by the union earlier in the negotiations. In fact, local union leaders wouldn't touch the final deal – it was negotiated by union officials at a district level.
"I wasted four months of my life," union member John Hunt told the Chicago Tribune after the contract was approved.
I write this without taking sides in any way. I have no doubt the previous, much more generous contract had indeed left Caterpillar in total paying far above "market wages." Union workers like nearly all the rest of us probably need to kick in a much bigger contribution for their healthcare costs.
But I don't think any of us can feel really good about asking workers hired before 2005 to take a six-year wage freeze, even if that's what it takes to bring the wage costs back to competitive reality.
But that's where we are right now. Labor related issues are everywhere in our supply chain – and current government agenda. It is tied in at the hip with jobs (or lack thereof) and the concern over the little progress the "middle class" has made in recent decades.
There appears to be a reasonable chance that dock workers at the 14 largest East and Gulf Coast ports will go on strike Sept. 30 (start making contingency plans right now, if you haven't – and realize it may not directly impact you, but could a key supplier).
The key issue: the port's desire to add lots of automation to of course reduce costs and but also make the ports more efficient. US ports are consistently criticized for their lack of global competitiveness. There are zero US ports near the top of the efficiency statistics. A few months ago, an executive from terminal operator APM noted that the company's facility in Yokohoma, Japan completes about 48 container moves per hour, versus just 25 or so for APM's terminal at Port Elizabeth, NJ - a difference of 92%.
That new automation will in the end certainly mean fewer dock workers are needed. Container volumes aren't going to increase 92% in the short term or anything like it. The union naturally enough wants to avoid or delay such automation plans. They are at an impasse. There may be a logistics-crippling strike. Then it will be a matter of who blinks first.
A report a few months ago from the Pacific Maritime Association, which represents ports in union matters on the West Coast, said that in 2011 a basic dockworker took home $129,000 in pay including overtime but not including benefits. I had a couple of Longshoremen write in challenging that number, but it is consistent with other data I have seen, and I assume is not that different on the East Coast as well. As I have written before it just seems odd to me that a worker can make that kind of money if he or she can just manage to get a dock job, while many union members in factories and elsewhere toil for just a small fraction of that kind of money.
To update some data from last year, the percent of private sector workers of all kinds that are in unions stayed the same at the end of 2011 as it was in 2010, at 6.9%. Even in the manufacturing sector, the rate has fallen to just 10.5%, versus 10.7% in 2011. There are about 1.4 million unionized workers in manufacturing, and that is actually up a bit from last year, as the total number of those employed in manufacturing has risen. I don't know quite how to reconcile the numbers, but workers in "production" occupations have a higher unionization rate, at 14.3%. 17.5% of workers in "transportation and material movement" occupations are unionized.
There are many union-related government issues out there, especially if Obama wins the presidential race, which I say just because it is clear an Obama administration would be more union-friendly than would be a Romney one. Those include the reasonable potential that the National Labor Relations Board (NLRB) might try after the election to find a way to get a form of "card check" rules through without action by Congress, as it did recently with approval of "microwave" elections that dramatically speed up the time from when unions get enough support to have a union election taken and when that vote occurs. Most believe the faster an election is held, the more advantage there is to the union.
Card check would take that one step further, eliminating even the need for a secret ballot on unionization by forming a union if a majority of workers sign basically a union support form. It is greatly feared by many companies.
There are other labor oddities, such as the long lasting, often under the surface battle between UPS and many union supporters in government trying to find a way to open UPS rival FedEx to get more unionized. So far, FedEx has beat back every challenge.
Of course, labor is now impacting supply chain network design, and the overall issue of US manufacturing. Less union-oriented right to work states in the South and Southwest have absolutely dominated major new factory announcements in recent years, including the Boeing plant in South Carolina that for a while the NRLB tried to shut down in 2010-11, on the grounds the aircraft maker moved work there from union-heavy Seattle plants illegally to punish the union. The issue was later made moot by a new contract in Seattle that allowed the work at the new plant. If that had not happened, the outcome of the legal battle between Boeing and the NLRB could have been seismic for US manufacturing if the government prevailed.
The much reported analysis from Boston Consulting Group in 2011 that predicted a "manufacturing renaissance" in the US based on manufacturing labor costs (wages times productivity) reaching parity with China by 2015 had a footnote not often cited: that the comparison was based on the most "competitive" regions of the US, which was basically the deep south. Whether it is China or Alabama, that is what the Cat workers in Joliet were in effect competing with. And that is just the way it is.
But I think we have hardly reached a crescendo. An article in the New York Times this week nicely summarized the already amazing developments that are happening in industrial robotics – and which are only going to accelerate. It cited a Philips Electronics electric razor factory in the Netherlands where some 128 robots perform intricate assembly operations 24 x 7. The plant employs about three dozen floor workers per shift there. A sister plant in China making the same basic products without the automation requires 10 times as many associates.
There are so many other issues: aging blue collar work forces, growing truck driver shortages likely to get worse, continued shortages in many skilled manufacturing positions that are leading some companies here to adopt Euro-style apprenticeship programs, distribution operations now looking at more automation – some very advanced – to reduce labor headaches…
If anyone else remembers seeing on TVLand or something the old Twilight Zone episode about a future factory that automates away its last worker let me know. Monday won't really be a good day for Labor.
Any reaction to Gilmore's Labor Supply Chain Report for 2012? What is your overall take? How do you see this playing out over the next 5 years? Let us know your thoughts at the Feedback button below.
|