I readily admit a certain fondness for the software category of Warehouse Management Systems (WMS), as it has a lot of ties to my earliest days in the business.
It’s an interesting application area for many reasons, not the least if which is that it is often devilishly hard to implement (I have the scars to prove it, though it is clearly getting better of late) and that despite being among the oldest of supply chain apps, it manages to sort of re-invent itself every few years.
That short intro to my column this week is tied to our latest issue of the Supply Chain Digest Letter, this time focused on Warehouse Management Systems. As always, if you didn’t receive a copy in the mail, you can download the pdf (SCDigest Letter on WMS) or visit the WMS Resources microsite, which has not only the Letter but white papers, case studies, articles, video – a sort of one-stop shop for those with any interest in the subject.
Gilmore Says: |
...A key step in the process has to be for the entire selection team to make some agreements about what capabilities are in scope and what are not.
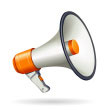
Click Here to See
Reader Feedback
|
In doing some research for this issue, I was amazed to re-discover how many companies are still running very old WMS systems, often dating back well into the 1990s. In fact, one very large consumer packaged goods company is still running a green screen system first stalled in 1992. Hope to write a little story about that one of these days – the company would love to replace it, but the effort to do so across dozens of warehouses always is just a bridge a bit too far.
But the WMS market is fairly hot again – the leaders and many others are clearly busy right now.
The history and pedigree of the WMS solution market is quite interesting, actually. There have been numerous acquisitions over many years, and knowing what actually happened to the WMS you may now still be running or have used in the past takes some real detective work, as does understanding the lineage of a new WMS you may be considering.
We are almost done with our “visual history” of the WMS industry to help understand all that, and hope to have it available very soon.
That history would include names like Exeter and RGTI and Worldwide Chain Store Systems and PCS– these and other WMS providers that came close to making it to the top of the industry but fell off the leadership train for one reason or another.
Ok, back to more substantive matters. The central challenge of WMS acquisition now is figuring out what you really want. Virtually every vendor now has a broad suite of applications, among which Warehouse Management is only one. There will likely also be Transportation Management, Labor Management, Slotting, Yard Management, Visibility, Scorecarding, Supplier Portals, and more.
How these applications are packaged may be different. Yard Management (YMS) may be just part of the WMS, or it may be a different module that must be licensed separately.
Pricing in this regard can also be a bit strange, but in the buyer’s favor. To put it bluntly, you will almost always pay a much lower price buying a Labor Management System (LMS) at the same time as the WMS than you will if you buy a stand alone LMS, or license the LMS at a later date after implementing the WMS.
I could explain why this is, but don’t have the room here. You can send me an email if you want more explanation.
So, as we say in the Letter, a key step in the process has to be for the entire selection team to make some agreements about what capabilities are in scope and what are not. We suggest identifying what components a company definitely wants to implement at the outset (say, WMS and YMS), what capabilities it definitely plans to implement but at a later date (say LMS), and what capabilities it is interested in but isn’t sure quite yet (say TMS or Visibility).
Getting this straight, or close enough (your views may change somewhat as the process unfolds) will provide a level of clarity to the evaluation process that is critical.
That’s in part because all these suites make the evaluation process much more complex. Not only do you have to do a deep dive on the core WMS, but also many of these other components as well to really compare different WMS or logistics suite providers. So to repeat, being clear about what you care enough about to throw in that hopper is a key first step – though WMS providers are quick to point out many less experienced customers often don’t understand the potential synergies across the suite components.
While the integration between components of these suites has become much better, just how deep and what benefits that integration brings can vary between different components within a given vendor’s full suite and certainly between vendors. Unfortunately, to understand that takes some hard work. Prospective WMS customers must develop demo scripts that force the vendors to show that integration, and to explain whether it is very basic or offers some “1+1 = 3” types of benefits.
Our colleague Mark Fralick, one of the industry’s true WMS experts, posits that especially today, companies need to think about WMS or a broader logistics suite more as a “platform” than a one-time investment with a sort of single ROI consideration.
Yes, that upfront investment analysis has to be done to get the funds, but the reality is that today, there is at least as much value in the right WMS and related components being able to provide the flexibility to quickly adapt to changes in the dynamic sea that is today’s distribution and fulfillment world.
“Take stock of your current WMS and logistics execution systems based on the idea that it will either help or hinder your ability to improve, adapt, and change with market forces,” Fralick says in the Letter.
The reality is that today’s WMS solutions have become incredibly more flexible than those of even the recent past, and the leaders all have “workflow” capabilities that allow companies to construct processes at the time of initial deployment or as things change without customization. It’s not perfect, but the capabilities are impressive.
Yes, some companies really are implementing WMS today with no modifications. Most often there still are some, frequently related to simply replicating some special way a company is doing things today in an area, or in getting the complex process of order release, picking and consolidation just right in a complex DC with multiple processing areas.
All of which says today the risk in WMS implementation has almost completely switched from problems with “the mods” not working right to the ability of the WMS vendor to manage the big effort to configure these complex systems correctly for a given DC.
And just as consolidation had left a relatively few number of major players left, along in the past year or two is coming a new wave of “on-demand” WMS players, some now sporting pretty impressive capabilities, and certainly potentially suitable for smaller or mid-sized DCs.
There is so much more in the Letter, but we are out of space.
Again, we encourage you to download the SCDLetter or visit the WMS Resources page. As always, welcome your thoughts, especially if you have recently implemented WMS.
Any reaction to Gilmore’s supply chain thoughts about WMS 2010? Let us know your thoughts at the Feedback button below.
|