That complexity can make it more difficult for effective margin management - and thus puts a premium on using more advanced techniques.
Interestingly, use of the more advanced tools tends to be greater among younger firms, publicly held firms, and firms for which private equity maintains a majority share. Older firms are generally less progressive in this area.
Margin maintenance metrics and tools are useful for managing margins: Almost all the tools included in the survey were ranked highly in terms of usefulness, but that often does translate into deployment.
For example, even though 73% of respondents said activity-based costing was useful, just 20% said they were using ABC. Similar ratings were generated for cost-to-serve, economic value-added, and balanced scorecard methods.
External constraints affect a firm's ability to manage margins more than internal constraints: In general, external constraints, such as the ability to raise prices, lower costs, forecast demand and others that are somewhat are largely outside the control of a company, are perceived as presenting greater hurdles to margin management than internal, more controllable factors.
Respondents indicated that internal constraints - such as access to technology and capital - generally do not hinder their ability to manage margins. Frankly, however, that seems somewhat contradictory to other data in the report. Companies may be over rating their abilities in this area.
Opportunities exist for middle market firms to embrace more sophisticated margin management tools: While just over half of middle market firms feel they have sufficient tools for margin analysis, the research shows that some of the highly effective margin management methods are used only sparingly.
Balanced scorecards are employed by only 31% of firms, activity-based costing by just 20% of firms (as noted above), and cost-to-serve models and economic value added analysis by just 14% of respondents.
Not surprisingly, firms that use more advanced tools are way more confident in their margin insights than those that use only more basic tools.
Because mid-market firms tend to be relatively fast growing versus larger firms, margin management might be even more important, the report notes, to help ensure that top line growth translates into a healthy bottom line.
But here there is a lot of variation, as shown in the chart below which illustrates which margin management tools are being used by what percent of mid-market companies.
Which Margin Management Tools are Mid-Martet Companies Using?
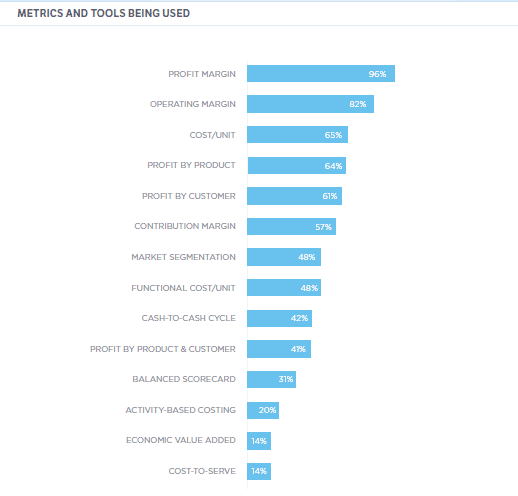
Source: National Center for the Middle Market
Naturally enough, what business sector a company is in impacts which tools it uses.
The report says that the usage of various margin metrics and tools varies based on where a company lies within the supply chain. Manufacturers are somewhat more likely to use basic tools such as cost per unit and functional cost. Given a sensitivity to inventory holdings, wholesalers are more likely to use cash-to-cash cycle.
Wholesalers are also more likely to use activity-based costing and balanced scorecard and to track profit by customer. Raw material suppliers appear progressive on contribution margin, profit by product by customer, and economic value add.
The report concludes by noting that "Findings from our focus group research indicated that those firms using methods like cost-to-serve modeling and balanced scorecard, among other advanced methods, believed that their use served as a source of competitive advantage when rivals failed to employ similar methods."
Why? Because understanding where a company's profits really come from can lead to better business strategy and investment decisions.
The report adds that the research "confirms that margin maintenance remains among the most pressing challenges for middle market companies."
Should Mid-Market Companies Use More Sophisticated Margin Management Tools? Let us know your thoughts at the Feedback section below.
|