SCDigest Says: |
3M's Littmann stethoscopes used to be made in steps involving 14 outside contractors and three 3M plants. Now all processes are being brought into a plant in Columbia, Mo. As a result, the cycle time will fall to 50 days from 165
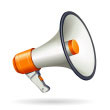
Click Here to See Reader Feedback
|
A simple story sums up the issue. 3M makes a line of a simple picture hooks under the Command brand name. Until recently, the production process in a sense started in an 3M adhesive plant in Missouri, from which the sticky stuff was shipped 550 miles to another 3M plant in Indiana, where the adhesive was applied to polyethylene foam.
From that factory, the work-in-process was shipped 600 more miles to Minneapolis, where a contractor applied the 3M logo and the WIP was sliced into the right sizes. From there, another 200 mile trip to a contractor that added the hooks and did the final packaging. 1300 miles of supply chain travel in total for a product that just sells for a few bucks.
The term "hairballs" for such supply chain complexity was apparently coined earlier by George Buckley, who recently retired after years as 3M's CEO and who launched a program to reduce some of that complexity.
John Woodworth, 3M's senior vice president of supply chain operations, told the Wall Street Journal that "We had long supply chains. It was and continues to be an issue."
Some complexity is inherent in a company that has some 65,000 SKUs across its many divisions, and operates 241 plants in 41 countries. Two-thirds of its sales now come from outside the US.
From our view, the complexity is perhaps at times compounded at 3M because a number of its businesses and plants are suppliers to other areas of the business, as locations and processes needed to support external customers can add complexity, time and distance for internal manufacturing flows.
The point person responsible for leading the war against hairballs is Jim Welsh, a vice president responsible for manufacturing and working with suppliers. He leads a team of 3M supply chain executives that is currently focused on 18 "high-impact" opportunities to improve efficiency in in manufacturing and supply chain.
The general goal is to reduce manufacturing cycle times by 25%.
"3M's long-term plan is to have fewer, larger, more efficient plants, and spread them out around the world," the Wall Street Journal article says. "More production will be done in what 3M calls "super hubs," plants capable of making scores of products for a region of the world. 3M now has 10 hubs, including six in the U.S. and one each in Singapore, Japan, Germany and Poland. It plans at least six more, all outside the U.S."
The hub strategy has already played out in the production of the Command picture hooks. In 2010, consolidated all the steps needed to make the hooks at a plant in Minnesota, where a number of products, such as Scotch tape, Nexcare bandages, furnace filters the hooks and other products are produced.
(Supply Chain Trends and Issues Article - Continued Below) |