In the end, BMW decided to try an experiment on one production line that produced rear axel gear boxes, and usually had about 45 workers.
The company asked for volunteers for the project, with a goal of replicating the expected 2017 age profile for the line workers. There was some derision at first, with the program quickly called the “pensioners line” inside the factory, but nevertheless a team of workers matching the 2017 profile was assembled without too much problem. The team consisted roughly half and half of workers that had already been on that line and new recruits for the program.
The key was an ambitious program where the line workers themselves came up with ideas to improve productivity on the line and/or the ergonomics of the work. Dozens of ideas were developed over time, within an open environment where “no idea is a bad idea” really did flourish.
As the ideas were collected on cards and pinned to boards, over time workers got the chance to vote on the priorities by being allocated a number of “points” that could be applied to a specific set of ideas. Those that garnered the most points were promoted to see if they could be implemented.
The program really took off, a BMS manager said, when an early idea to add wood floors to some of the work cells instead of concrete was implemented.
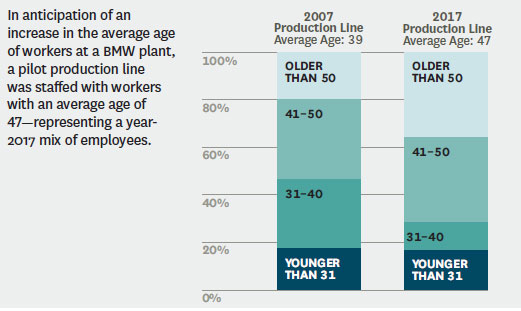
Source: Harvard Business Review
“People from neighboring lines laughed at first, but after only one day it became clear that it helped,” the HBR article quotes one manager as observing. “At the end of the day, your knees were not aching. This showed us that the 2017 project could make sense.”
With that early success, on total some 70 ideas were eventually implemented on the gear box line. They ranged from giving workers more orthopedic footwear to changing the angle on computer monitors to reduce neck strain to changing the grips on certain tools.
The company also started more aggressive job rotation practices as well, especially not allowing workers to stay on the most physically challenging jobs for long periods of time.
The total investment was quite modest – just some $20,000 euros for the line-related changes, and another $20,000 euros for the time employees spent in the meetings.
While it can never be clear exactly the role the line changes played versus other factors, line productivity in the end improved 7% within a year, reaching the levels achieved by lines with younger age profiles. Line about, per previous targets, was increased from 440 units per day to first 500 and then 530 per day, which was achieved with almost zero defects. The productivity gains meant this could be done with four fewer workers, but that decrease faced challenges – no one wanted to leave the gear box line.
Absenteeism has also dropped.
BMW has since rolled out the program to workers in other factories in Germany, Austria, and the US, where similar results have been achieved.
Perhaps the key point: there kinds of improvements in ergonomics and productivity likely could not have been realized from a top-down approach, but only through direct line workers involvement.
What’s your reaction to the BMW story? Has your company down anything similar? How big a factor will the aging workforce be? Let us know your thoughts at the Feedback button below.
SCDigest is Twittering!
Follow us now at https://twitter.com/scdigest
|