|
|
|
|
 |
Supply
Chain by the Numbers |
|
|
|
- May 24 , 2012
|
|
|
|
|
|
|
|
US Factory Utilization Almost All the Way Back; SAP Reaches Deep in Wallet for Ariba; TVs being Made Again in America; Amazing Level of New Truckload Fleets
|
|
|
|
|
|
|
$499 |
The projected price for a new television that – believe it or not – is being made in the US. That is the first time TV assembly has been done since the last major TV major factory in the US was shuttered about five years ago. The new 46-inch flat screen will be sold initially at Target stores, and is the result of an unusual alliance between a US brand-focused company (Element Electronics of Eden Prairie, MN) and a Chinese supplier of many of required components (Tongfang–Global). The “labor cost differential isn’t as great as it once was,” said the head of the Consumer Electronics Association.
|
|
|
|
|
|
|
1.7
|
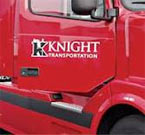
|
The incredibly low average age in years of the fleet of truckload carrier Knight Transportation, according to its recent Q1 earnings call. Knight is among several major TL carriers that haveturned over a huge percent of its existing trucks in the last two years. Those moves have been driven by new environmental requirements and the opportunity for improved fuel mileage. Just a couple of weeks ago, for example, Schneider National said it would acquire 3000 new tractors in 2012, replacing one-third of its fleet.
|
|
|
|
|
|
|
|
 |
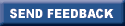 |
|
|
|