This week, I am again thinking about "the ASN," otherwise known as the Advance Ship Notice or the EDI 856 transaction.
To me, the ASN is one of the definitive "best practices" of an integrated supply chain. It is what links the flow of goods between supplier and customer. While really a B2B concept, in a sense even we as consumers demand and now receive an ASN when shopping on-line, getting detailed emails about order status from the retailer and detailed delivery status from UPS or FedEx.
I have been following ASNs for years, in part because my early career in the supply chain and for some time thereafter was heavily involved in the first years of the retail initiatives around electronic ASNs tied UCC-128 serialized shipping labels. As I have noted before, I would have guessed then, circa 1992, that we would have near ubiquitous use of ASNs by 2010. Alas, it wasn't to be, though we are making progress.
Gilmore Says: |
The ASN should be and often is a key element of the "perfect order." To be a true perfect order, the ASN should exactly match what is received and also perfectly match the invoice.
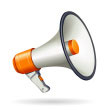
Click Here to See
Reader Feedback
|
So, just to get everyone on the same page, the ASN is - sort of - like an electronic packing slip sent by the shipper/supplier via EDI, web email or other means in advance of its customer receiving the goods. Useful under any circumstances, the ASN when tied to unique (serialized) identifiers (bar code labels, soon RFID) on pallets and cartons can drive important logistics and supply chain benefits.
The practice and opportunities of ASNs vary a by industry sector, but there are several consistent themes. The first is the ability to dramatically reduce receiving costs (generally thought by about 40% or so); second to understand if there is a discrepancy between what is expected and what has been shipped, enabling the receiver to react accordingly (such as changing production scheduling); third, a variation of number 2 unique to retailing, the opportunity to re-allocate the goods that will be shipped to stores based on knowledge of actual fill rates against the PO; fourth, improved ability to cross dock - among other supply chain benefits.
The ASN should be and often is a key element of the "perfect order." To be a true perfect order, the ASN should exactly match what is received and also perfectly match the invoice. I would add that the ASN should also beat the physical delivery, which can sometimes be a problem. All that, as we will discuss in just a second, is still not at all easy to achieve by suppliers.
There are in fact all kinds of questions/issues around perfecting the ASN. For example:
- At what level is the ASN built? For instance, some companies only get an ASN at the truckload/shipment level, not at the pallet level, or the pallet level but not at the carton level. The greatest potential benefits are from the most detailed ASNs, naturally.
Do companies really understand the quality (ASN = Shipment = Invoice + received prior to delivery) on either the shipper or the receive sides of the equation?
New evidence raises concern about that last question. Next week, in fact, we are hosting a Videocast featuring brand new research by Drs. Brian Gibson and Brent Williams of Auburn University about the state of ASNs in the consumer goods to retail supply chain. While not wanting to give away too much before the broadcast, one finding is that there is still a significant discrepancy between what is on the ASN from the consumer goods manufacturer and what shows up on the retail dock. (To register for the Videocast, go to: ASN Research Videocast; all registrants will also receive a copy of the final report when it is issued in early November.)
That more formal research insight was backed up by my friend Kevin Harris of Compliance Networks, who says that as part of a service where his company does basically data entry for freight bill information for retailers, it is obvious to them that in many cases ASNs and what was received are not in sync. Easily visible to the human eye.
How big a problem is that? I am not exactly sure, but the analogy I would use is reject cartons in a distribution sortation system (i.e., cartons that don't scan or get sorted right, going down the dreaded "jackpot line" for manual handling); even a fairly small number of such cartons can cause real operational headaches; I think it is likely the same for receipts that don't match the ASN.
So what are the factors that go in to how accurate a company's ASNs are versus what is actually received (including timing issues)?
I have been pondering this, and come up with these factors (from the receivers point of view):
Focus/attention/measurement: Where does this issue rank in supply chain priorities, and what measures are used to track it? Are specific goals set, and does some individual own that number?
Receiving unit profile (pallets, cartons, split case, etc.): Clearly, it is harder to pick and pack mixed-SKU pallets or split case cartons than it is to load full pallets, leading to picking/packing errors which in turn lead to bad ASNs. Full pallet receipts should much more likely match the ASN than thousands of split case cartons simply due to human picking errors.
Vendor profile: I will say, perhaps wrongly, that larger suppliers with more sophisticated systems are more likely to get ASNs right than smaller companies; offshore suppliers add a whole other dynamic.
Level of ASN audits and other internal processes: Highly related to point 1, audits of receipts at some level and using that insight (see next point) to understand the true state of affairs and drive improvement has to be a key factor.
Remedial action/closed loop processes: ASN accuracy will vary by vendor, type of handling unit, even by supplier DC making the shipment. It may vary over time for shipments from the same vendor. What processes the receiver uses to create a closed loop system (chargebacks, inclusion in vendor scorecards, direct discussions, vendor training, etc.) should have a big impact on ASN accuracy over time.
Network issues: Specific to timing, how a receive handles incoming ASNs (e.g., batch processes) can affect the timing, especially when suppliers are nearby. I worked with a beverage company once which was blaming suppliers for late ASNs, only to later find the enemy was themselves due to processing times.
So that's where I am leaving it today. More thoughts after we hear the research. But I will still maintain that getting ASNs right is essential to getting to the next level of supply chain excellence.
What are your thoughts on ASNs and their accuracy? Would you add any factors to Gilmore's list? Do you see ASNs as improving or stuck on a plateau? Let us know your thoughts at the Feedback button below.
|